S&P 500 Companies Sound Alarm on Coronavirus Impact on Earnings, Profits
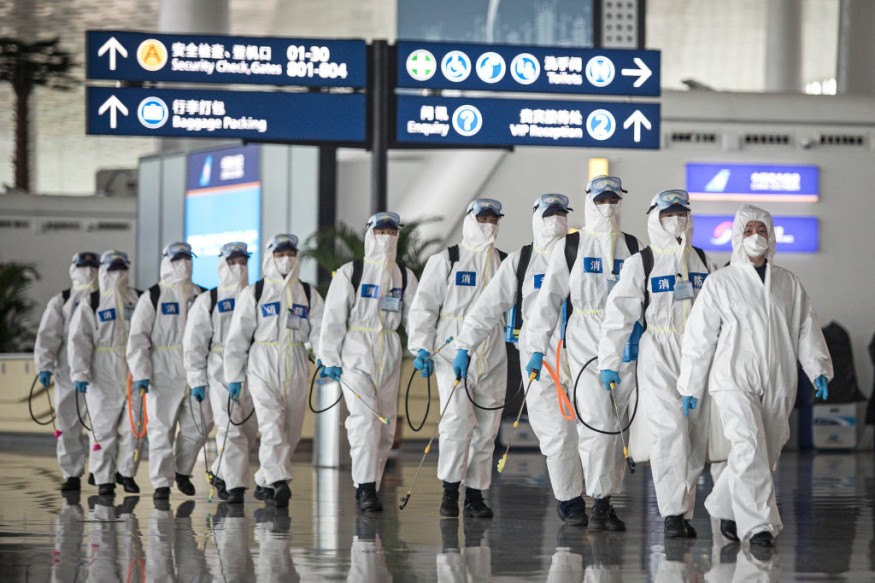
The coronavirus outbreak in China is predicted to have a significant impact on the revenues and profitability of nearly one in five S&P 500 corporations, indicating the disease's widespread effects on enterprises worldwide.
A CNBC review of more than 180 business announcements and earnings transcripts from the start of 2020 showed considerable worry.
Although the majority of management teams that have issued revenue warnings have stated that they do not anticipate any effect on full-year results, several have projected a first-quarter decline.
Precautionary cancellations are anticipated to cost Royal Caribbean Cruises 65 cents in full-year earnings per share, the firm announced earlier this month.
Others, such as Apple, stated that in order to account for the possible impact, they have released revenue ranges for the first quarter that are wider than typical.
It's too early to determine if the coronavirus would affect current-quarter finances, according to a significant number of S&P executives did not include in its current tally. However, they did vow to update stakeholders if the situation changes in the coming weeks. A few have acknowledged closing their locations in China, including McDonald's.
Global Supply Chains
The coronavirus outbreak in China has had significant ripple effects on global supply chains. With China being a major hub for manufacturing and production, the shutdown of factories has disrupted the supply of essential components and products across various industries. Companies that rely heavily on Chinese manufacturing are facing delays and shortages, which have cascading impacts on their operations worldwide.
For example, the automotive industry has been particularly hard hit, with major car manufacturers experiencing delays in receiving parts and components. This has led to temporary production halts and a slowdown in vehicle output. Similarly, the electronics sector, which depends on Chinese factories for the production of semiconductors and other critical components, is grappling with supply constraints that threaten to delay product launches and reduce inventory levels.
Alternative Sourcing Strategies
In response to these disruptions, companies are actively seeking ways to diversify their supply chains and reduce their dependence on a single source. One strategy involves shifting production to other countries. For instance, some firms are increasing their manufacturing capacity in Southeast Asian nations like Vietnam and Thailand, which are emerging as alternative production hubs.
Companies are also exploring partnerships with suppliers in different regions to create a more resilient supply chain network. This includes establishing relationships with manufacturers in North America and Europe to mitigate risks associated with geographic concentration.
Additionally, businesses are investing in technology and automation to enhance supply chain visibility and flexibility. By using advanced analytics and real-time monitoring, companies can better predict disruptions and respond more swiftly to changing conditions. This proactive approach allows firms to adjust their sourcing strategies dynamically, ensuring a steadier flow of materials and products.
The content provided on MoneyTimes.com is for informational purposes only and is not intended as financial advice. Please consult with a professional financial advisor before making any investment decisions.
© 2025 MoneyTimes.com All rights reserved. Do not reproduce without permission.